Mesh Belt Continuous Bright Hardening and Tempering Plants
Introduction:
Of all types of continuous furnaces, wire mesh belt furnace , of modern design, is emerging as the most popular choice.
These Furnaces are marginally more expensive than shaker hearth furnaces, but relative movement between the hot component and the conveyor is avoided as are problems associated with wrapped shaker hearth plates. The component residence time in a shaker hearth furnace (especially at the start and end of run) cannot be guaranteed as is mesh belt furnace.
In shaker hearth the hearth plate weighing around 100 kgs for 'MB-300' width furnace is to be heated, where as in mesh belt furnaces are designed with "hot belt return" feature. In this design the furnace is constructed such that the returning hot belt travels below the cold belt entering the furnace.
The construction of the front end of the furnace is such that the bulk of the heat contained in the returning hot belt is transferred effectively to the entering cold belt and the component on it.
The system is effective enough to preheat the core of the components upto 600°C before they enter the furnace hot zone. Apart from energy saving this preheating also reduces component distortion. The geometry of the entry section of the furnace will also cause preheating by the velocity of the out going hot protective atmosphere gas which also serves to drive out water or oil vapour that may be carried in with the components.
Consistency of quality is better obtained when components are continuously quenched, a few pieces at a time instead of in a batch at periodic intervals. Of the total tonnage of heat treated components the majority do not require fixturing and can tumble into a quench tank.
The ideal plant for all such components in terms of quality, capital cost as well as operating cost, is a continuous conveyorised heating and quenching system. Components spend less time at temperature and consume less energy compared to batch furnaces. Continuous quenching, a few components at a time, ensures a high degree of quality consistency in terms of hardness, case depth and physical properties.
Capability:
Bright hardening, carburising and tempering of mass produced components like bearing rings, fasteners, chain parts, circlips, hose clamps, etc.
Hardening Furnace
TMax 950°C with protective/reactive atmosphere, with thyristor control.
Oil Tank
with Mesh Belt Conveyor, heat exchanger, cascade curtain, in-line filtration and a novel component handling system of very low distortion.
Tempering Furnace
TMax 650°C, Pit type with baffle and centrifugal blower.
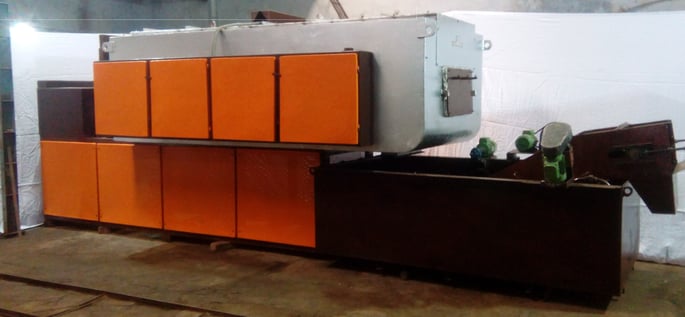
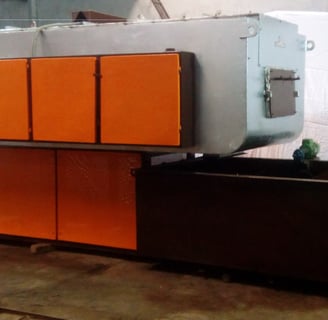
About Us
Om Furnaces and Ovens is one of the leading manufacturers on Industrial Furnaces and Ovens, based out of Umbergaon, Gujarat.
Established in 1982, we have emerged as as a principal in market and have been setting new benchmark with our offerings and services.
Inquiry
© 2024. All rights reserved.
Our Other Products
Tempering Furnace Ageing Oven
Gas Fired Furnaces - Batch Type Drying Oven
Rotary Hearth Furnace Continuous Oven
Salt Bath Furnace
Pit Furnace
Stress Relieving Furnace